Guitar
Maton 'Phil Manning' Re-Fret
I get a lot of enquiries about re-fretting - what's involved, how does it affect the guitar's sound and playability? So when this rather nice old Maton came in for a re fret I took the chance to take a few photos.
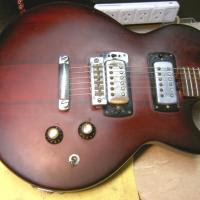
This is not too good a picture of it but its gives an idea. The guitar is from the mid 70's and its been used a lot. Usually I find guitars like this one that show evidence of a lot of playing are good ones. Bad guitars just don't get played as much! The bridge isn't original and touches the bridge pickup so that's getting replaced too. I get a lot of my parts from http://www.guitarparts.co.nz/ - Iain who runs it is a lovely bloke and always gets stuff to me the next day. He does the 'Allparts' range which I love.But the main problem with this guitar is of course the fret wear. Not only are there deep dents in the frets around the open D chord but lots of wide flat areas all over the neck. I can tell its been owned by a pretty good player - blues/rock style I'd guess by the wear from a wide vibrato and string bending.If the wear isn't too deep it could be fret stoned out but with this one there's no chance of that. When the frets are this flat the guitar always sounds dull and lifeless. With a rounded, polished fret the string has a 'point' it can vibrate off instead of an indefined flat area.As frets get older their seating in the slot can get a little sloppy and absorb instead of transmit string energy. A lot of 'dead spots' on necks that get blamed on inconsistancies in the wood are really just loose frets.
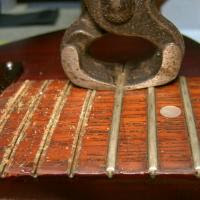
Re-fretting always makes a guitar sound better.The first part of the job is to remove the old frets. I do this with a pair of pincers that I've ground to be flat on the face. This means I can get right under the fret more easily. Its quite a delicate operation because I don't want to pull any wood up with them. These frets are still well seated which is nice to see considering they've been in there since the mid 70's.
The nut needs to be removed and in this case replaced. These days I often use to use 'Graph TechTusq' for nuts and acoustic saddles. Their 'string saver' saddles are excellent too. I remove the nut with a thin, narrow (1/8") chisel I made specially for the job. Its a tool I made when I was in college about 15 years ago and its served me well. This bone nut isn't held on too tightly and comes off easily.
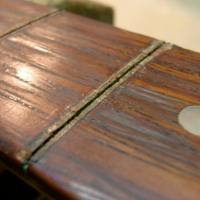
So the board is now fretless and ready for leveling. In this pic you can see how dirty the wood is from years of playing and some of the dents in the board from long fingernails. I level the board using a glass plane. This is a sanding block made of toughened glass so its pretty flat. Different grades of abrasive paper can be attached to it to sand the board level.
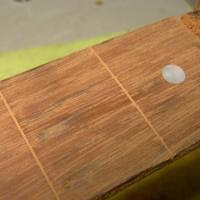
This is an essential part of the process. If the board isn't level then when I do the final skim of the fretshave to take out any unevenness on the frets. I don't want to put wear into new frets. This pic is taken half way through the leveling - you can still see wear in the board.
I sand through the grades of paper all the way to 1000 grade. Between sanding I wet the wood with water and leave it to evapourate. This 'fluffs' the grain out and gives a finer finish. After 3 or 4 times the wood doesn't expand any more and its oh so smooth!
The final stage before actually fretting is cleaning out the slots.I use a little saw that I've added a depth-stop to so I only go as deep as I need to. Maton have used a glue in the fret slots which needs cleaning out. Its a method I prefere to use myself and its good to see them doing it - most manufacturers don't bother. You can see how much better the board looks after its sanding.
Fretwire comes in a lot of different sizes. After a long discussion with the owner of this guitar, playing his rather nice Thinline Tele and having him play my Strat he decided on narrow jumbo wire. Its the same width as old style Fender wire but its higher. He's a good player and likes to bend strings so high wire is a good choice. With high frets your finger tip touches less wood which makes string bending a lot smoother.
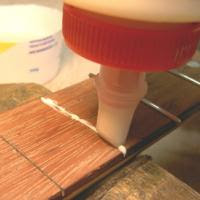
A lot of players like high frets - I'm one of them. As I mentioned earlierI like to put glue in the fret slot. I use an alaphatic resin (Titebond). Its a water based wood glue that goes brittle hard when set. Now I'm not trying to glue the fret in - sticking wood to metal using wood glue is a dead loss. I do it to fill any gaps there might be under or around the fret with something hard. When the fret goes in on top of the glue it pushes it into every gap including into the wood end grain inside the fret slot. This gives the fret a very firm connection to the wood of the board and to the neck and of course makes a difference to the tone. The better the fret is seated the more lively and responsive the guitar is.
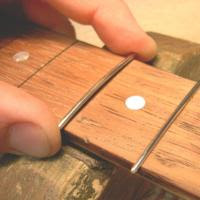
Ok so here's the fun bit! I put the frets in by the old method of tapping them in with a fret hammer. I first curve the fret to a tighter radius than the board ( so the ends sit down nicely).I very gently tap the ends into the slot just enough to hold the fret in.
I use a fret drift (block of mild steel) to even out the hammer pressure. The neck is supported with a neck rest that has a leather pad to protect the finish. I do this over the most solid part of the work bench (over a leg) so the hammer blows are 'dead'. If you have to hit the fret more than a few times then you end up loostening it. You can hear when its gone in true - there's a lot of experience and feel involved.
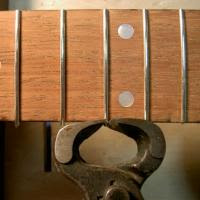
I leave the glue to dry for a few hours and then cut the fret ends off using my pincers again. Then its a case of filing the fret ends. This is one of the most time consuming and fiddly parts of the job and the hardest to describe. Not only does the angle need to be cut but the ends filed smooth so there are no sharp edges. And of course there are usually 44 of them. Then its a fret stone (http://mrglyn.blogspot.co.nz/2012/01/fret-stone-fender-stratocaster.html), oiling the board and setting the instrument up. I use "Luthiers Fines' fretboard oil - www.luthiersfinest.com it's available through me at my workshop or www.guitarstuff.co.nz
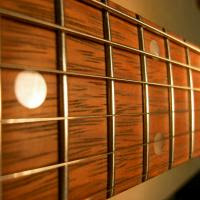
There's a lot of work in a refret but the end result is a completely new playing surface, better tone and response and of course giving your instrument many more years of service.
………………………………………………………………………………………….
Feel free to contact me about repair work (if you are in NZ). I only check emails weekly so the workshop phone is always the best 09 307 6501.
Workshop Hours
Mon……. 8-6
Tues……. 8-6
Wed…….. Closed
Thurs …..8-6
Fri ……….8-6
Sat/Sun ..Closed
Mr Glyn’s Guitars
21a Khyber Pass Road
Auckland
New Zealand
http://www.mrglyn.co.nz/
www.facebook.com/MrGlynGuitars
www.mrglyn.blogspot.com
09 307 6501, 021 912678
-
Stainless Steel Fretwire
I get often asked 'what's the difference between normal frets and stainless steel?'. I first used stainless steel fretwire in '08 when a customer requested it and now offer it as an option when re-fretting. For most players new frets...
-
Music Man Stingray V De-fretting
I got a call the other day from Matt from the Auckland Rockshop - "can I de-fret a Music Man Stingray 5 string Bass for them?" Well in fact he said "what will it cost?". This is a job I do from time to time so I thought I'd write...
-
Scalloping A Fingerboard
I have customers who play all styles of music and this one is most definately ROCK. It can be such a treat having great musicians playing in the workshop, just showing me what's wrong with their guitars or trying them out after I've worked on...
-
Gibson Es125d Re-fret
This is a continuation of my post describing a re-fret. This nice old Gibson is from 1966 and had such fret and finger board wear that I just had to show you it. The serial number isn't too clear in the photo but its 433265 and according to Gibson's...
-
Fernandes 'v' Ebony Fingerboard
This week I've had a lot of work on - a Hagstrom in need of re-wiring, a telecaster neck pickup to re-wind, A Les Paul to set up as well as the more run of the mill stuff. But the main job has been to replace the fingerboard on a Fernandes 'Flying...
Guitar