Guitar
Scalloping a fingerboard
I have customers who play all styles of music and this one is most definately ROCK.
It can be such a treat having great musicians playing in the workshop, just showing me what's wrong with their guitars or trying them out after I've worked on them. I get to see them close up so I can analylize their playing style to get the set up just right for them. I love my job :-)
This customer came to the workshop interested in having his fingerboard scalloped from 12th fret up. This is something I'd only recomend having done for players with a high level of technical skill. Check this guy out on YouTube http://www.youtube.com/watch?v=JaIKzC8xPFM he's got a very accurate right hand and a light, precise touch with his left. After seeing him play I had no hesitation in agreeing to do the job.
The idea behind scalloping is to remove wood from between the frets.
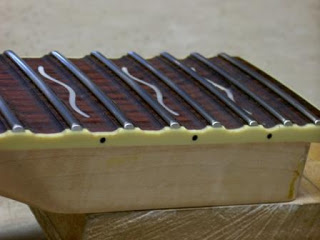
This means that the player's finger tips don't touch the wood at all making vibrato and string bending a lot smoother. Right hand tapping techniques are easier too - with a right hand tap and pull off its the pull off part that can often be weak. With a scalloped board the finger can get under the string more and 'pluck' the string more easily
It all sounds great but there can be problems if the player squeezes too tightly with the left hand - this can bend notes very sharp and sound terrible especially with chords
So I always ask a few questions and watch the customer play before doing this job. If they don't like it there's no turning back.
I've seen a lot of boards (and frets) ruined by enthusiastic amateurs attacking the guitar with a file to try and scallop it. I do the bulk of the job with a router and the neck held firmly in a jig. I want the finished job to look neat and even, not like there's been an accident.
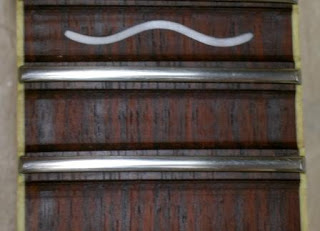
I leave a gap either side of the fret which makes no difference to the feel for the player but makes re-fretting easier.
Without this gap when the frets are pulled out huge chunks of fingerboard wood can come out too. This way the frets have more support and the board stays in good condition.
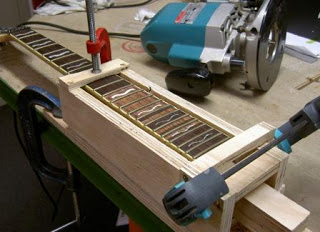
I clamp the neck in a special jig I have made specifically for scalloping. It holds the neck firmly and has a movable fence to guide the router. This way I can cut the scallops evenly and at the same depth as well as following the profile of the fingerboard. I use a rounded cutter in the router to give a nice smooth curve to each scallop. This is a pretty time consuming job and requires a great deal of accuracy.
The router is a great tool and does a very neat and consistant job but needs to be treated with respect. When I used to teach guitar making at The City of Leeds College of Music i used to say to my students 'no-one ever had a minor accident with a router'.
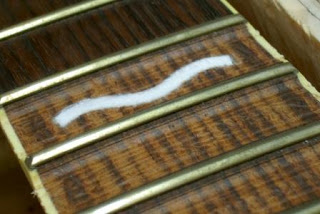
This is the finish I get with the router. The shape is there but its a bit rough. I finish it off with a cabinet scraper and with fine sandpaper.
After this I give the guitar a light fret stone just to make sure everything is even so i can set it up with a low action.
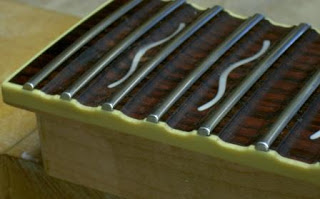
With the frets polished and the board oiled I'm pleased with the end result.
The player likes it too - he's brought me in two more guitars to do, another Ibanez and an Axis.
Might get some of my work shown off on You Tube soon.
………………………………………………………………………………………….
Feel free to contact me about repair work (if you are in NZ). I only check emails weekly so the workshop phone is always the best 09 307 6501.
Workshop Hours
Mon……. 8-6
Tues……. 8-6
Wed…….. Closed
Thurs …..8-6
Fri ……….8-6
Sat/Sun ..Closed
Mr Glyn’s Guitars
21a Khyber Pass Road
Auckland
New Zealand
http://www.mrglyn.co.nz/
www.facebook.com/MrGlynGuitars
www.mrglyn.blogspot.com
09 307 6501, 021 912678
-
Fret Stone - Fender Stratocaster
Frets wear. Eventually they wear out and need replacing. If the wear is not too deep the frets can be ground down to the lowest point of the wear, re-crowned, polished and the guitar is ready for a few more years playing before re-fretting. This is called...
-
Stainless Steel Fretwire
I get often asked 'what's the difference between normal frets and stainless steel?'. I first used stainless steel fretwire in '08 when a customer requested it and now offer it as an option when re-fretting. For most players new frets...
-
New Zealand Music Month
. I'm going to do my best to get out and see more live music in May. There are so many of my customers I've never seen play live.Check out http://www.nzmusicmonth.co.nz/ for what's going on.Looks like I'm in for a busy month keeping...
-
Gibson Es125d Re-fret
This is a continuation of my post describing a re-fret. This nice old Gibson is from 1966 and had such fret and finger board wear that I just had to show you it. The serial number isn't too clear in the photo but its 433265 and according to Gibson's...
-
Fernandes 'v' Ebony Fingerboard
This week I've had a lot of work on - a Hagstrom in need of re-wiring, a telecaster neck pickup to re-wind, A Les Paul to set up as well as the more run of the mill stuff. But the main job has been to replace the fingerboard on a Fernandes 'Flying...
Guitar