Guitar
Guild D40 bridge saddle
This is a beautiful Guild D40 from 1977.
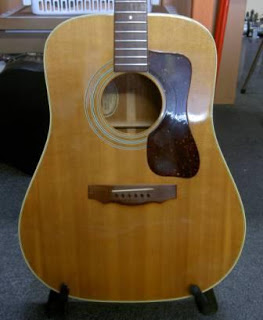
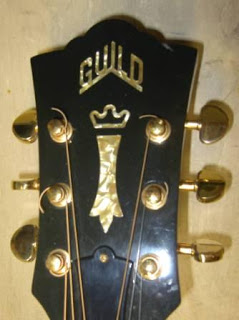
The customer is a pro player and bought the guitar new in Sydney. It hasn't been played a huge amount and its in great condition.
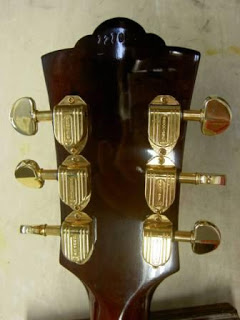
The problem is with the intonation - its not out a huge amount but enough to annoy the player who has a very sensitive ear.
So we decided the best solution was to fit a compensated bridge saddle. I also suggested a compensated nut but he doesn't like the look of them.
String compensation and tuning can be a complicated and frustrating subject so I'll save the details for another time and just give a simplified version. All guitars (especially steel strung) need at least a little bridge compensation to play in tune. The reason for this is in the playing action. To play a note (other than open) you need to press the string down onto the fret. Lets say the string is 2mm from the top of the fret - you bend the string (sharp) by a distance of that 2mm before you sound the note. Try fretting a note then bending the string by 2mm - you can hear it. So to compensate for this the string length is made slightly longer by moving the saddle back thus putting the note in tune again. Its made slightly more tricky by the fact that bending a thicker string by the 2mm will sharpen it more than a thinner string - so thicker strings need to be compensated more. Also wound strings react differently to plain ones. So if you change your action, string gauge or tuning you'll need to change your intonation. Another thing worth remembering is its all just compromise, you cannot play exactly in tune - there is no exact - with the limitations of action and equal tempered tuning you can get pretty close but never exactly in tune in all keys. I'll go on about this more another time because its a bit of a pet subject of mine - but anyway, back to the Guild.
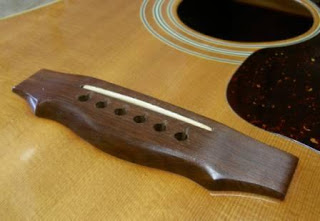
The original saddle is straight and made of bone. It is a little too low to be used again so I'm going to make a new bone saddle. Bone is the best material for saddles, I get mine from guitarparts.co.nz usually, its at the right price, he nearly always has stock and it arrives the next day. Bone is certainly not the easiest material to work with, it's very hard and the dust isn't too pleasant. I always wear a mask when working with it. This is partly because the fine dust can be harmful and partly because it is exactly the same smell as when the dentist is drilling your teeth. Not something I want to be reminded of.
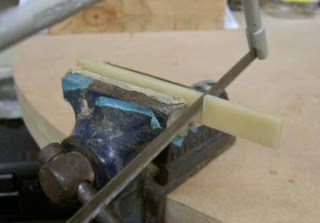
I start off by cutting the saddle to length with a junior hack saw. I cut it close to the vice jaws to lessen the chances of the bone snapping. Bone it brittle stuff. I leave it slightly oversize so I can sand it to an exact fit later.
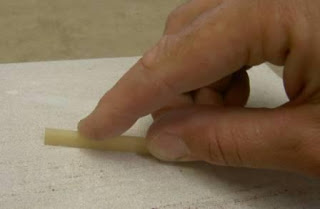
To sand the saddle I use a sheet of abrasive paper (about 80 grit) attached to a piece of mdf with double sided tape. The mdf has a kind of handle built in so it can be easily clamped to the work bench. With this I can get the bottom of the saddle flat and true. The bottom must be a right angle to the side for the saddle to connect properly with the bottom of the saddleslot and therefore to the guitar top. This is especially critical if there is an undersaddle piezo pickup fitted.The saddle must be a snug fit in the slot so it doesn't leanf orward under string tension. If it is too tight a fit it can get wedged in and not connect properly with the bottom of the slot. Its worth spending time on the fit of the saddle.
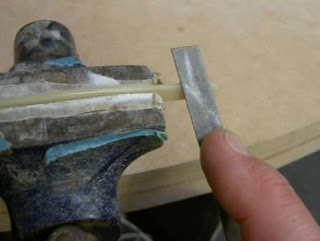
Once I'm happy with the way the saddle sits in the slot I can shape it for height to set the action. As I am replacing a perfectly good saddle I have one to copy. So I sand the new saddle to be about 1/2mm higher than the old one. Then its a case of filing the top of it to achieve the compensated intonation. The 6th string (bass E) is set to the back of the saddle (maximum string length) and the G string to the front with the D and A set in between creating a smooth line on the top of the saddle.The B is set back and the 1st string forward.
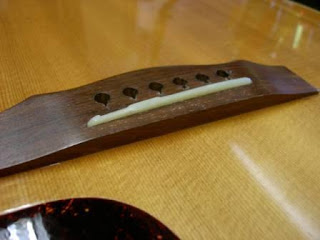
Once the filing is finished I sand any scratches out of the bone with 800 wet'n'dry and then 1200 after which I polish it up with some burnishing compound. I love polished bone, it brings out the warm colour of it. The player uses D'Addario 12's which are great strings. I get a lot of my strings from http://www.guitarstuff.co.nz/ they do a really good range at an amazing price. The delivery is cheap and next day. It means I don't need to leave the workshop to get them too. The last thing is to tune her up and check the intonation. Its a lot better than it was according to the Peterson tuner and to my ears. The customer was very happy with it though I still think it needed a compensated nut as well - ha ha
………………………………………………………………………………………….
Feel free to contact me about repair work (if you are in NZ). I only check emails weekly so the workshop phone is always the best 09 307 6501.
Workshop Hours
Mon……. 8-6
Tues……. 8-6
Wed…….. Closed
Thurs …..8-6
Fri ……….8-6
Sat/Sun ..Closed
Mr Glyn’s Guitars
21a Khyber Pass Road
Auckland
New Zealand
http://www.mrglyn.co.nz/
www.facebook.com/MrGlynGuitars
www.mrglyn.blogspot.com
09 307 6501, 021 912678
-
Acoustic Guitar Pickups - Lr Baggs Anthem
I often get asked what the best system is for amplifying an acoustic guitar. My answer is usually - how much do you want to spend and what do you plan to do with it? For recording I would always use an external mic (mixed with a touch of pickup...
-
Gibson Tennessee Nut Repair
This is an unusual guitar - It's a 1990 Gibson Tennessee Chet Atkins model. Here's the serial number, the first and fifth number tell me the year. I think it was '76 they started this system. Gibson's website is good for dating...
-
Stringing A Guitar
I come across a lot of guitars that have been strung badly. If the strings are not put on correctly there is little chance of the instrument staying in tune. Its surprising how many players get it wrong - even pros. The idea is to get at least 3 tight,...
-
Reverend 'warhawk' Set-up
I do a lot of work for 'poolside studios'. They importvarious makes of musical stuff including 'Top Hat' amps, 'Eastwood' guitars and 'Reverend' guitars. All their guitars that come into New Zealand get checked over by...
-
Yamaha Fg-260 12-string
This is a lovely old guitar that came to me with an unplayable action. 12 string guitars often suffer from problems related to string tension and this one had really suffered. The top was bellying and needed the bridge plate replacing - I'll go into...
Guitar