Guitar
1967 Fender Jazz Bass: Rebuilding a water-damaged rosewood veneer fretboard
I took this project on more as a challenge than as a typical repair - not sure how much I'd charge to do it
again, but almost certainly A LOT more than I did in this case I'm documenting ! That being said - this repair does show the resiliency of Fender necks and that almost anything can be repaired on them.
The subject of this post was a 1967 Fender Jazz bass neck that had apparently suffered water damage and then gradually started to fall apart over the years. It came as part of a package of parts that a client purchased off Ebay from a guitar repair shop that was clearing out some long dormant projects.
When I received the neck: it was missing a chunk of the rosewood fretboard veneer and one fret at the end of the neck, most of the frets were loose, and some of the binding near the nut was missing. And obviously the green nut was NOT original ! Once I started examining and wiggling the frets it became obvious that not only were the frets loose, but so was a significant portion of the rosewood fretboard !!
After removing some of the loosest pieces of the fretboard, I considered just pulling all the frets up until the 9th fret - and flowing some thin super-glue under the loose portions of the fretboard and clamping it all together and hoping for the best.
But first I took the neck to my friends at Mouradian Guitar Repair, in Winchester, Massachusetts for some consultation. John Mouradian pointed out that a lot of the fretboard appeared loose and bowed up from the neck - and that the maple strip covering the truss rod also appeared loose. He told me that I had to make sure that strip was glued back in place - without mucking up the trussrod in the process - so I should take off as much of the rosewood veneer as was loose - and maybe consider planing the neck down for a new slab board. Though that would be labor intensive as well - since a new board would have to be cut for inlays and binding.
I decided to take a different approach - in an attempt to keep as much of the neck original as possible. I would take John's advice, and remove all the rosewood and inlays that were at all loose - and repair the truss rod overlay - but then I'd REINSTALL the pieces of the original rosewood and inlays - dress the fretboard make sure it was good and flat - and then re-install the original frets and binding.
So I started by removing the binding on the neck - which came off easily with a little warm alcohol/water solution brushed into the seam and a razor blade to gently pry it loose. I then began working under the rosewood veneer with a razor blade - also flowing in some alcohol and water to try to soften the hide glue - and work my way up from the bottom of the neck.
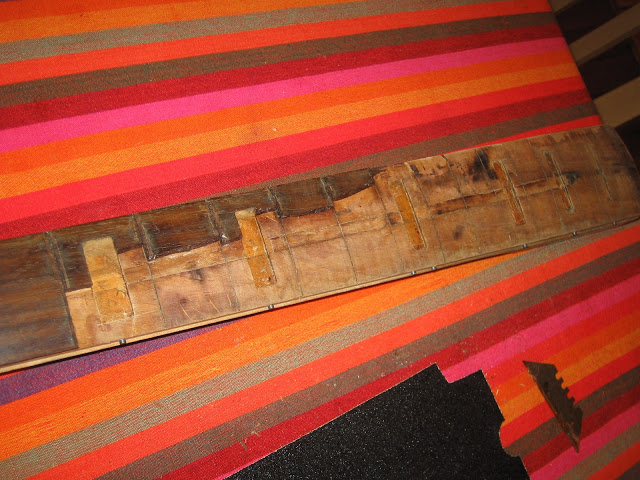 |
Loose bits peeled off - note that I left the side dot markers in place !! |
As I made my way along the neck - the first pieces came off easily - and note that the veneer was basically sliced into rectangles by the fretslots - the fret slots actually bottom out in the maple of neck! As I got up towards the 15th fret though, the rosewood started putting up more of a fight - and was cracking into pieces as it came off - with some sections along the treble side of the fretboard remaining very securely attached. The inlays also proved inconsistent - with some easily popping out and some cracking or requiring a lot of force and prying with a narrow chisel to remove them.
I used a large piece of masking tape to fix the removed pieces in order for later reinstallation.
Finally however, I had everything loose off the neck - and had about 40% of the truss rod overlay exposed - and it was obviously quite loose and popped up from the surface of the neck. I ran a razor blade down the seam of the truss rod overlay to make sure there was some room to work some glue in.
I used Titebond wood glue - working it in with my fingers - it will actually push into the small gap, but unlike superglue, it won't be drawn in by capillary action - and therefore the Titebond won't glue up the truss rod - which would keep the truss rod from working evenly. (tip o' the cap to John Mouradian for that advice !)
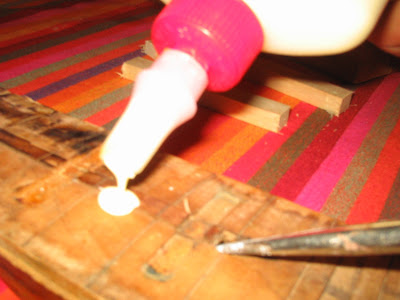 |
Applying Titebond |
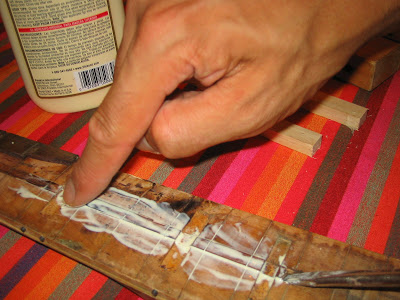 |
Working the glue into the seams |
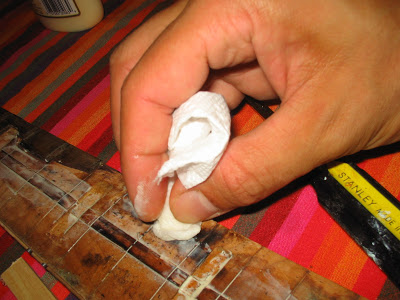 |
Using a slightly damp paper towel to remove extra glue |
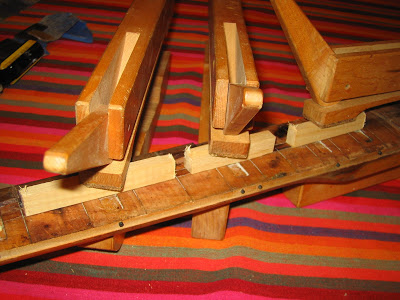 |
Clamping the overlay in place - small strips of waxpaper are under the wooden cauls |
I did slightly tension the truss rod after the glue had dried for a day - just to see if the overlay had glued in at all - and it didn't budge. I didn't want to push my luck though, as I figured re-gluing the rosewood and inlays onto the neck would further reinforce the truss rod overlay.
Now came the time to put the puzzle back together !!
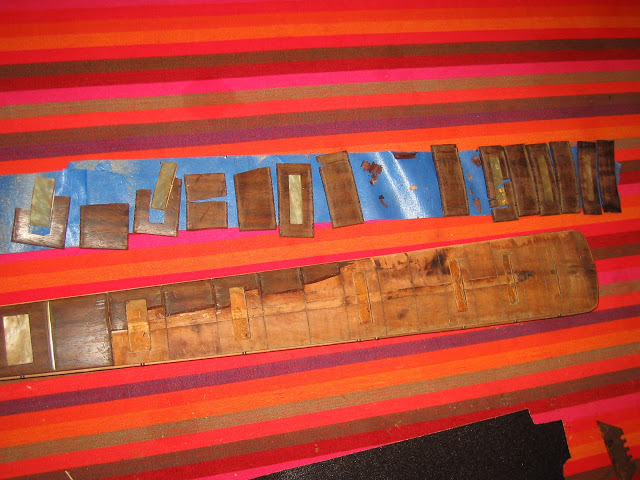 |
A jigsaw puzzle !! |
First I had to clean the old glue off the inlays - as well as repair one of the inlays that split (used superglue). I scraped and sanded the undersides and didn't worry about the tops, since I'd be leveling the fretboard later.
I used Titebond glue to reglue the pieces of fretboard and inlays - making sure that the joined edges also had glue - and then wiping the extra off the surface of the board with a damp paper towel.
Titebond has a pretty long working time, so I was able to glue all the rosewood pieces and inlays in place before I gently clamped everything down with a 7.25 in radius block - with waxpaper between the block and fretboard. Note the lines between the pieces of rosewood in the picture above.
Remaining chips and gaps were filled with a combination of superglue and rosewood dust, and hit with accelerator spray. Then the defretted portion of the fretboard was sanded with the same clamping block to level out everything. The view below is after sanding - note the new piece of rosewood added at the very end of the fretboard.
Several more stages of sanding, working down to 600 grit paper - and then some Olde English scratch polish oil to show the results. Even the new piece at the end of the neck matches pretty well. And you can barely see the lines where the rosewood veneer cracked and was reglued ! Even the repaired inlay looks intact !
Prior to reinstalling the original frets, I lightly recut the fret slots, as they had glue in them from the repairs. I also straightened any kinks in the frets and then over bent them a little at the ends to make sure they fret ends wouldn't pop out. I reinstalled the frets with a light bead of Franklin Hide Glue along the tang of each fret - and then once again used the 7.25 inch radius block to clamp the frets in place.
One new fret was installed at the highest position (the shiny one !) and then filed down to match the height and width of the old frets. As you can see - the fretboard looks pretty consistent - with the gaps and seams being all but invisible ! The third inlay from the left was the one that was cracked.
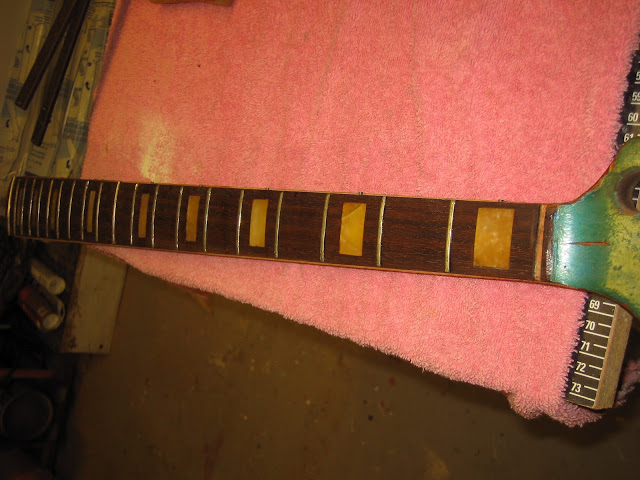 |
The other end of the fretboard - that LPB headstock will be getting a little cleaning up too !! |
Finally, I reinstalled the original binding, which had a split at the very butt of the neck above the truss rod adjustment - probably from some shrinkage and was missing a short segment on the bass side near the nut. I spliced in a small segment of new binding and lightly tinted it with some lacquer - the splice was visible but at least the neck felt right now in the first fret position.
Regular Duco plastic cement was used, though straight acetone will also work. The Duco glue will fill more gaps and has a longer working time. The old side dots made placement of the binding on the bass side of the neck very easy - the binding just snapped on over the dots - almost like two Lego pieces going together!
 |
The replacement piece of binding, shaped to follow the contour of the headstock |
Meanwhile - the body had undergone its own restoration - and had the Lake Placid Blue finish heavily ambered to match the very green headtsock - I think I did a pretty good job at matching !!
All in all a fairly challenging piece of work - I think in the future I'd instead replace ALL the frets and sand the entire fretboard after the repair work to really get everything as level and even as possible and to start off a new with fresh frets.
That being said, the bass played very well and had no twist or bow under tension - I had to go back and file a few frets here and there to get the action low, but that's to be expected in most refrets and especially in a case where half the fretboard is re-assembled from fragments !!
Next up - I have to figure out how to fabricate a new veneer fretboard for an Olympic White headstock 1966 Fender Jazz bass neck I have lurking around ....
-
Hofnerarchtop - Neck Problems
I see quite a few old Hofners, it's amazing how many are still around. It is, however, unusual to see one that had not had a neck break at some time in its life. This one has not only had the typical break but it's been repaired badly....
-
Fender Bronco Fretboard Repair
This one is a 'real' repair, in the sense that something is broken. Its a Fender Bronco which is an instrument I very rarely see. It is by no means a new guitar but it still gets regularly gigged and toured with NZ punk band Die!Die!Die! http://en.wikipedia.org/wiki/Die!_Die!_Die!...
-
Saving A Fretless, 9-string 1963 Fender Jaguar Neck !!
A friend of mine was able to purchase a "project" Jaguar for a very reasonable price - the Jaguar was fitted with a WD replacement neck but also had the original and much abused neck sitting in the case. I decided to see if I could repair the original...
-
For Sale: 1963 Vox Bassmaster Bass, English-made
Here is a very very rare bass from the early days of Vox/JMI - the short-scale Bassmaster. Vox began as an amplifier company in the late 1950s, based in Kent, England - but around 1961 they decided to branch out into electric guitars and basses. These...
-
Updated! 1966 Gibson Thunderbird: Gluing Back Together The Bits And Pieces!!
< This is one of the most ambitious rebuild projects I have undertaken yet - perhaps THE most ambitious - and it remains to be seen how it works out in the end. This is a project for a client - my friend David from New York, who owns the Guild Starfire...
Guitar